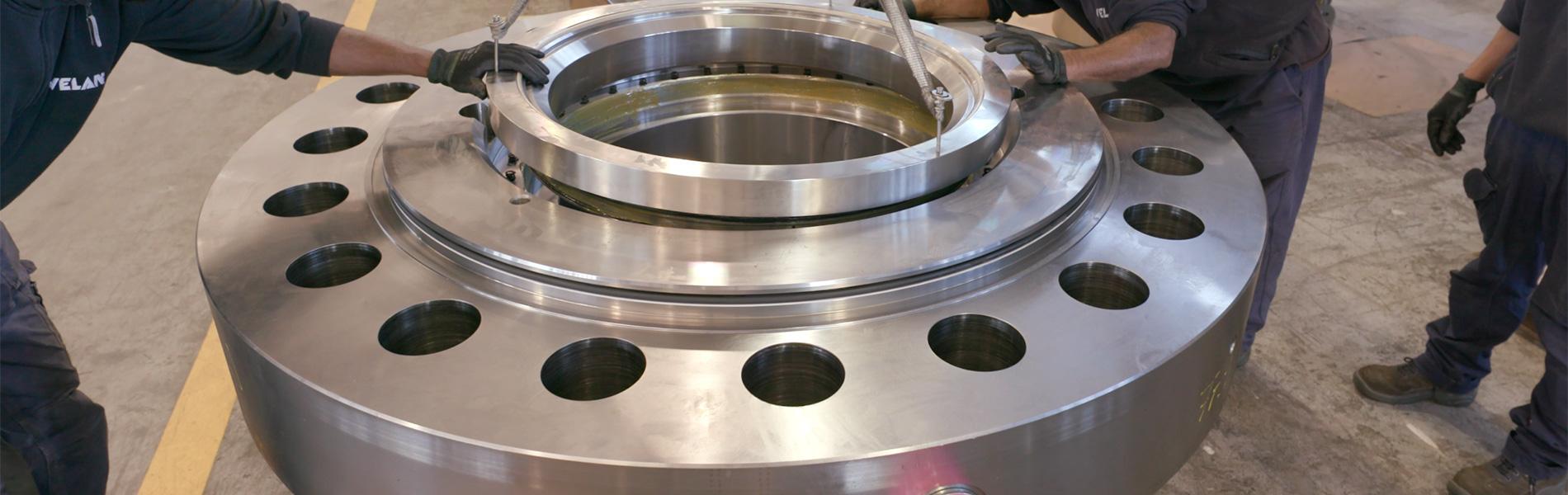
Cryogenic top-entry trunnion ball valve
API 6D Top entry ball valve
8 inch. ASME 600, buttwelding connections, Operated by bare stem
HIPPS CRYOGENIC with Design T. -196°C
Cryogenic top-entry ball valves
from 3 to 24 inch. ASME 900, Butt weld connections, opertaed by Gear
in critical LNG fields
Testing cryogenic top-entry ball valves
from 3 to 24 inch. ASME 900, Butt weld connections, operated by Gear
in critical LNG fields
Testing cryogenic top-entry ball valves
from 3 to 24 inch. ASME 900, Butt weld connections, operated by Gear
in critical LNG fields
Testing cryogenic top-entry ball valves
from 3 to 24 inch. ASME 900, Butt weld connections, operated by Gear
in critical LNG fields
TYF-TYS
based on BS 6364, MESC 77/200, ISO 28921 (on request) and customer requirements
NPS 2 -36 (DN 50-900)
RF, RTJ as per B16.5 &B16.47
BW, Butt Welded as per B16.25
Forged or cast one-piece
Soft or metal seated with hard facing on Ball and Seats
Seat design to avoid trapped fluid in body cavity
Secondary seals in pure Graphite
Anti-static device
Anti-blowout stem
Lip seal configuration
Low fugitive emission stem packing available
Special maintenance tool for in-line seat disengagement
Extended bonnet for low and cryogenic service
Manual: wrench or gear with padlocking
Actuated: Pneumatic/ Hydraulic/Electric
Compliance with BS 6364, MESC 77/200, ISO 28921 (on request) inspection and testing
Fire safe and fire tested as per API 6FA/607
SIL 3 Certification as per IEC61508
Fugitive Emission as per ISO15848
PED 2014/68/UE
Compliance with BS EN 1626 standard (available on request)
Compliance with BS EN 12567 standard (available on request)
Cryogenic top-entry ball valves are manufactured for extremely low temperature and cryogenic applications where in-line disassembly is required for trim inspection and maintenance.Valves are designed with an integral bonnet extension which prevents cryogenic liquids from reaching the stem packing by enabling the liquids to boil and convert to gas. This minimizes the energy loss along the extension and protects the valve from malfunctioning. The structural integrity of the valve reduces any thermal deformation of internal components caused by temperature variance to a minimum, ensuring the highest level of performance for tight shut-off in critical LNG fields.